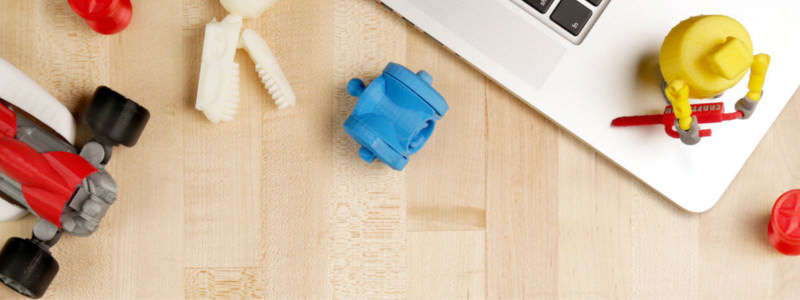
CNCフライスを買った大きな目的として、基板を作ることがあります。
といってもプリント基板を業者に発注するのも安くなってきましたし、そんなにメリットはないのですが・・・
それでも1枚しかいらないときや、プロトタイプを作ってみたいときには有用だと思います。
スポンサーリンク
回路を書く
どういうもの何を作ろうか考えましたが、やっぱり一番最初の自作基板ということでLチカ回路でしょう。
検索してみるとわんさか出てきます。
適当に目星をつけて、それをEagleで書きます。
はい、書けました。
基板を作って動かなかった嫌なので一応ブレッドボードで試しましたよ。
ブロッキング発振回路というやつです。
点滅というよりフラッシュという感じですけど、構いません。
基板を設計する
ボード図の作成
次に基板を設計します。
と言っても適当に配置して自動配線するだけです。
線の間隔などのデザインルールはデフォルトのままにしています。
ちょっと線は太いほうが良いと思いますが、テストなので「これくらいでできたらいいなあ」という願望も含めて何もいじりませんでした。
ドリルで穴を開けたくなかったので部品はほとんど表面実装部品を使っています。
電源用のコネクタだけはなかったので穴を開ける工程が入ってしまいました。
Gコードの生成
Gコードの生成は探してみるとEagleのスクリプトにありました。
PCB-GCodeといやつで、読んで字のごとく書いた基板からGコードを生成してくれる便利なものです。
詳しい使用方法は省きますが、ざっくりとだけ。
というより私も分かっていません(笑)
詳細はまた記事にでもしようと思います。
(1) 最新版をダウンロードしてEagleのulpフォルダに回答した中身を全部入れます。
pcb-gcode-3.6.2.4 というバージョンであればそのフォルダの中身(pcb-gcode.ulpなど)全部をulpのフォルダにいれます。
(2) brd編集中にEagleの上のメニューにある、Run ULP をクリックして pcb-gcode-setup.ulp を選択します。
(3) するとウィンドウが出てくるので、削る深さやドリル径などを設定したら Accept and make my board というボタンをクリックしてGコードが書かれたファイルを生成します。
よく分かってませんので、上記の設定があっているか自信がありません。
ここで生成したファイルを基板製作にそのまま使用します。
基板製作の準備
面出し
CNCフライスはあるものの、このまま生基板をセッティングして削るとテーブルの傾きの影響でうまく削れません。
自作なのでまったく平行ではないんですよね。
そこで面出しというものを行います。
板を敷いて、それを削ることでZ軸に対して傾きのない平面を作ります。
この時は Heightmap という項目に気付いていましたが、めんどくさそうだなあと思って避けていました。
実はこれをちゃんと設定してあげると、面出しはほぼ必要なさそうですし、むしろもっと綺麗に基板を作れますが今回は設定しません。
面出しのGコードは以下のサイトで生成致しました。
これをフライスを動かすソフトウェアで読み込んで、動かします。
板は塩ビです。
アクリルのほうが粘っこくなくて良さそうですよね。
もったいなくて使わなかったんですが。
ちなみに110mmx60mmくらいで40分ぐらいかかりました。
思ったより傾いていてびっくりしました。
X軸の調整がすぐにでも必要なレベルですね。
左右でおよそ1mmの差があるという。
角度計もあったほうが良さそうです。
エンドミルは写真に写っているものではなくて、ストレートのエンドミルで削っています。
スポンサーリンク
これで安い方なんですから、機械加工は恐ろしいです。
エンドミルをセット
面出しが終わったら、生基板をセットします。
固定は両面テープですよ。
そして、エンドミルを生基板に近づけます。
今回は加工するもの表面が金属なので、テスタで導通を見ながら近づけます。
プローブがあれば、もっと簡単なのでしょうか。
一応注文はしましたが、来るのは1月末くらいになるでしょうね。
ちなみに、この時はA5ピンにクリップの片側をつなげれば自動でセットできるのを知りませんでした・・・
基板製作
これでようやく基板が作れます。
生成したGコードのファイルを読み込んでみます。
おお!なんだかそれっぽい形になっています、すごいですね(他人事)
そして[Send]ボタンを押してCNCフライスに命令を送ります。
待つこと5分程で基板ができました。
微妙に銅箔が残っちゃいました。
今回は深さを0.1mmにしましたが、もうちょっと深いほうが良さそうです。
出来上がったので、周りを切り落とします。
よく見ると繋がっていそうなところやバリがありますね。
ダイヤモンド刃ではなかなか切れませんでした。
ベークライトを初めて切ったのでびっくりです。
配線はちゃんと独立していまして、どこも導通はありませんでした。
ビギナーズラックでしょうか。
最後にドリルで穴をあけます。
面倒くさいのでピンバイスを使って手作業であけました。
ちょっと大きすぎましたかね。
周りの銅箔はまだ残っているのでギリギリセーフとしましょう。
そして、はんだ付けです。
部品点数が少ないのであっという間に終わります。
やはり電源用のコネクタ部分で失敗してしまいました。
なんとか接続できましたが、もうちょっと小さい穴の方が良かったですね。
その他の部品は何も問題なく付けることができました。
基板を動かす
なんと一発で動きました!
超簡単な回路なので当たり前ですよね・・・。
簡単なプロトタイプ基板なら、CNCフライスを頼っても良さそうです。
両面基板は流石に難しいと思うのでやめておきます。
次は大きな部品を使う基板で、ドリルを使って穴あけをしてみたいと思います。
スポンサーリンク
Leave a Comment